数控双头车床作为现代制造业中重要的高效加工设备,其性能优化对于提升生产效率、降低生产成本、提高产品质量具有重要意义。通过对其结构、工艺、控制系统以及辅助设备进行优化,可以有效地提升其加工效率和稳定性,从而实现生产过程的智能化与自动化。以下是
数控双头车床性能优化的几个关键方面。
一、双主轴配置的优化
其核心优势之一在于其双主轴设计。通过两个主轴同时进行加工,能够显著减少工件重新夹持和转动的时间,提高了加工效率。优化双主轴之间的协同工作,通过合理的工艺规划,可以实现同时加工不同区域的不同工艺,避免了不必要的空闲时间。
二、控制系统的智能化优化
数控系统是决定车床加工性能和精度的关键部件。提升控制系统的智能化水平,是实现生产效率提升的重要手段。随着人工智能、机器学习等技术的发展,越来越多的数控系统开始具备自适应调整和故障预测的功能。通过在数控系统中引入先进的算法和实时数据分析,车床能够根据加工过程中的变化自动调整加工参数,从而提高加工精度和效率。
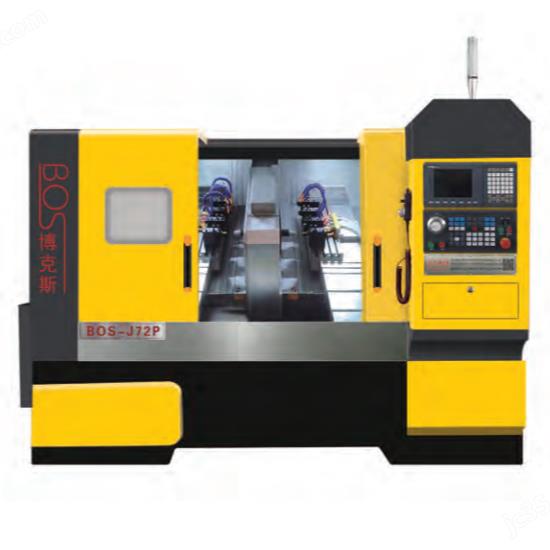
三、刀具管理与切削工艺优化
刀具是影响加工效率和精度的重要因素。在性能优化中,刀具的选择与管理是提升生产效率的关键。首先,选择高性能、适应性强的刀具可以提高加工过程中的切削效率,并减少刀具更换的频率。此外,采用刀具在线监测系统,可以实时监控刀具的状态,包括刀具磨损、破损等情况,及时进行刀具更换和调整,避免因刀具问题导致的加工不合格。
四、自动化与协作系统的应用
随着制造业自动化水平的提高,自动化与协作系统在数控双头车床中的应用越来越广泛。通过引入自动化装料、卸料和切换系统,数控车床能够在没有人工干预的情况下自动完成整个加工过程,提高了生产的连续性和效率。自动化系统能够准确快速地完成工件的装夹和卸载,减少了人工操作所带来的不确定性和误差。
五、加工环境的优化
加工环境对其性能有着直接影响,特别是在精密加工过程中,环境的稳定性至关重要。通过优化车床的工作环境,可以有效降低因环境变化导致的加工误差,提高加工质量。此外,采用先进的冷却系统可以降低切削过程中的热负荷,减少热变形,进一步提高加工稳定性。
数控双头车床的性能优化是一个综合性的问题,涉及到硬件、控制系统、工艺、自动化等多个方面。通过优化双主轴配置、提升控制系统智能化水平、优化刀具管理、应用自动化系统、改善加工环境以及进行实时数据监控,可以显著提高生产效率。